Custom Connector Pins
Without the Waste
The days when you had to choose between speed, cost, and precision are over.
Electropin has leveraged the power of cold-form manufacturing to become an unrivaled provider of custom connector pins. Simply put, we can make your pins faster, more accurately, and at less cost than anyone else because we produce no scrap.
So stop paying a machine shop to waste metal with every pin they make for you. With Electropin, get the custom connector pins you need without compromising on cost and quality.
Why Are You Still Paying to
Send Metal to the Scrapyard?
cut the source material to make your part. This causes you a lot of costly problems.
Batch Consistency Over Time
Because the tool’s cutting edge changes with every part, the pins from the beginning of the batch won’t match the ones from the end.
Producing Scrap
Wastes Materials
Every time you cut metal, you’re producing scrap. That’s metal you pay for but delivers value to the scrapyard instead of to your customers.
Tooling Edges
Get Dull
Cutting will dull your tools’ edges, resulting in more frequent and costly retooling.
Automatic Die Rolling: Your
Solution to Wasteful Machining
Automatic die rolling is a cold-form manufacturing technique that doesn’t just minimize the problems of machining: it eliminates them.
That’s because the process is based on pushing whatever raw material you choose into a custom die and forcing that metal to conform to the shape of the die.
With no cutting, there are no blunted parts or wasted scrap. And with no need to heat the material, you can get as many as five custom connector pins a second—with no waste.
Cold-Forming Your
Custom Connector Pins Is…
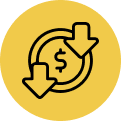
Inexpensive
With cold-forming, when you pay for five pounds of material, you get five pounds of pins. Plus you don’t have to worry about regular (and costly) retooling.
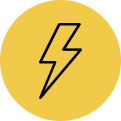
Faster
Machining can only produce a pin as fast as a blade can cut through metal. With cold-forming, you can get up to five pins a second.
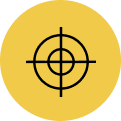
Accurate
Because cold-forming tools don’t dull, you can get an error rate of just one pin per 600,000,000. And no, that’s not a typo. No other method of making pins even comes close.
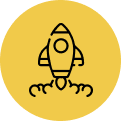
Dynamic
Sometimes you can get your first batch of cold-formed pins in just two weeks. And when the raw materials are available, you can dramatically scale up production when your needs change.
The Cold-Forming
Process
Don’t know if cold-forming is the best manufacturing technique to meet your needs? That’s OK! We’ve developed this customized process to help you get the high-performing pins you need without sacrificing any functionality.
01
Step 1: Discuss Your Performance Needs
03
Step 3: Create
a Die Mold
Electropin’s experts will create the tools needed to cold-form custom connector pins to your specifications.
02
Step 2: Refine
the Design
If cold-forming is feasible for your pin, an Electropin engineer will work with you to refine your design to achieve all the functionality you need at minimal cost.
03
Step 3: Create a Die Mold
Electropin’s experts will create the tools needed to cold-form custom connector pins to your specifications.
04
Step 4: Cold-Form
Your Parts
Electropin will begin to manufacture your parts in as little as two weeks, delivering batches of pins on the timeline that works for you.
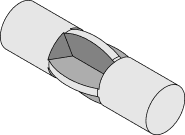
Star
Electropin’s most popular feature, a star provides the highest retention and anti-rotational strength for your pin.
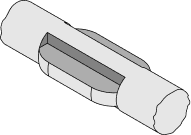
Tabs
Splines offer strong retention with minimal expansion of the pin’s diameter.
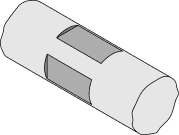
Inscribed Square
Inscribed squares offer retention and anti-rotation without any protrusion from the diameter of the pin.
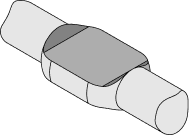
Flat
Flat features make a pin that, once inserted, is hard to pull out or rotate.
What Are People Saying?
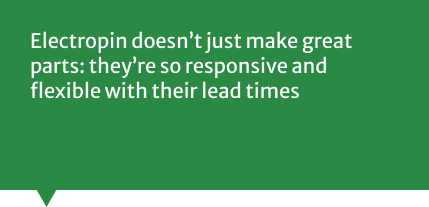
Lou Guerci
President @ Bead Electronics